Rigging Accident Prevention: Ensuring Your Team’s Safety
Safe lifting of materials is a base of many industries, however, it involves risks. A variety of factors, including environmental circumstances, equipment failure, and human error, can cause accidents.
Understanding the Common Causes of Rigging Accidents
Environmental Factors: Unexpected weather conditions, crowded job sites, and unstable ground can increase risks.
Equipment Failure: Damaged rigging equipment, overloaded cranes, and excessive loads.
Human Error: Miscalculations, improper lifting techniques, and poor training.
Top Strategies for Rigging Accident Prevention
Detailed Risk View: Perform careful risk checks for every rigging job. Spot potential dangers and put safety measures in place.
Specialized Training: Ensure all rigging personnel undergo intensive training covering safe lifting techniques, equipment examination,and emergency procedures.
Regular Equipment Examination: Set up a detailed check program for all rigging equipment, such as slings, chains, hooks, and shackles.
Load Capacity and Stability: Always observe equipment load limits and ensure proper load distribution. Avoid overloading and unstable loads.
Clear Communication: Set up clear communication channels between crane operators, riggers, and ground personnel. Use standardized hand signals and communication protocols.
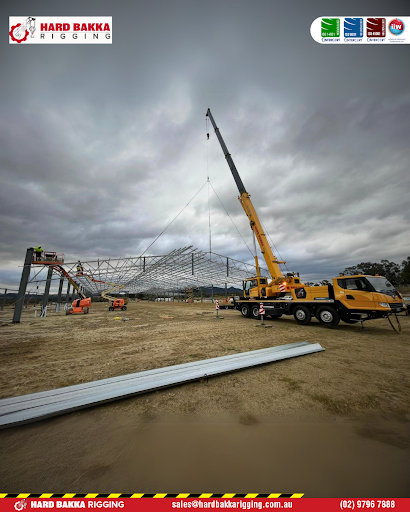
Understanding Common Causes of Rigging Accidents
In rigging operations, accidents can arise from various factors. To prevent accidents, it’s crucial to understand these risks and how they occur.
- Environmental Factors: Weather and job site conditions can play a big role in rigging safety. Wind, rain, and unstable ground are common risk factors. High winds can destabilize lifted loads, while uneven ground can increase the chance of cranes and equipment tipping. Regular weather checks and site assessments are essential to ensure safe working conditions.
- Equipment Failure: Rigging equipment must be in excellent condition. Worn or damaged slings, overloaded cranes, or improper use of hooks and shackles can lead to equipment failure. Ensuring all equipment undergoes routine maintenance and is replaced when damaged is vital for accident prevention.
- Human Error: Miscalculations, poor communication, and lack of training are common contributors to rigging accidents. For example, incorrect load estimation or improper securing of loads can lead to accidents. Rigging personnel need proper training, and communication protocols should be in place to minimize human error.
Top Strategies for Rigging Accident Prevention
Implementing safety measures helps prevent accidents and protect the workforce. Here are key strategies to reduce risks in rigging operations.
1. Risk Assessment and Planning
Every rigging operation should begin with a thorough risk assessment. Identify potential hazards such as site limitations, environmental conditions, and load specifics. Use a checklist to document each risk and establish controls to prevent accidents. Planning can include:
- Identifying hazards related to site and equipment.
- Setting up clear safety protocols.
- Developing a response plan in case of unexpected risks.
2. Specialized Rigging Training
Training is essential for all rigging staff. Employees should be well-versed in safe lifting techniques, equipment handling, and understanding load capacity. Effective training programs include:
- Load Calculation and Capacity: Teach workers how to assess load weight and select appropriate rigging equipment.
- Equipment Inspection: Train staff on proper inspection techniques for identifying wear and tear on slings, hooks, and other equipment.
- Emergency Response: Ensure that all personnel understand what to do if an accident occurs on-site.
3. Routine Equipment Inspections
Regular inspections of rigging equipment prevent accidents due to equipment failure. Establish a routine checklist that includes:
- Daily Pre-Use Inspections: Check for visible damage, wear, or improper alignment.
- Periodic Maintenance: Schedule regular maintenance for all equipment, such as slings, chains, and cranes.
- Documentation: Keep detailed records of all inspections, noting any repairs or replacements made.
4. Load Capacity and Stability Control
Overloading equipment is a common cause of accidents. Ensuring that loads are within the safe capacity of each piece of equipment is crucial. Follow these guidelines:
- Calculate Load Weights Accurately: Use load charts to understand the weight limits for each crane or rigging device.
- Balance and Secure Loads: Uneven or improperly secured loads can shift, causing instability. Verify that all loads are balanced and secured according to the manufacturer’s guidelines.
5. Clear Communication and Signals
Miscommunication can lead to serious accidents. Set up standardized communication methods to ensure clarity between operators, riggers, and ground personnel:
- Standard Hand Signals: Use universally recognized hand signals for basic crane and rigging commands.
- Radio Communication: Provide radios or headsets to all rigging staff on-site, especially when visual contact isn’t possible.
- Clear Instructions: Confirm instructions with each team member, especially during complex or high-risk lifts.
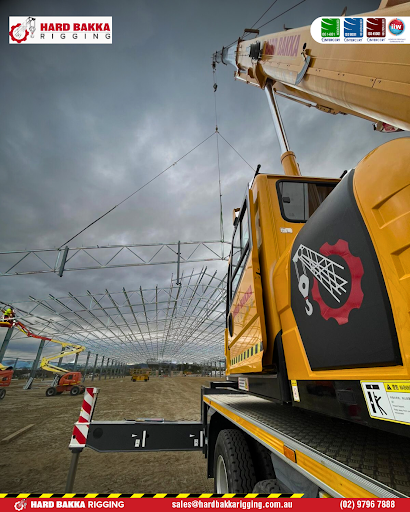
Frequently Asked Questions (FAQs)
Q1: What are the primary causes of rigging accidents?
- Answer: Rigging accidents are commonly caused by environmental factors like weather and unstable ground, equipment failure due to wear or overload, and human errors such as miscalculations and poor communication.
Q2: How often should rigging equipment be inspected?
- Answer: Rigging equipment should undergo daily pre-use inspections and scheduled maintenance checks. Regular documentation helps track wear and prevent accidents due to equipment failure.
Q3: What kind of training do rigging personnel need?
- Answer: Rigging personnel should receive specialized training on load calculation, safe lifting techniques, equipment inspection, and emergency response to ensure safe operations on-site.
Q4: What role does communication play in rigging safety?
- Answer: Clear communication between crane operators, riggers, and ground personnel is crucial. Standard hand signals, radio communication, and clear instructions help prevent miscommunication that could lead to accidents.
Q5: How does Hard Bakka Rigging ensure safety on job sites?
- Answer: We prioritize safety by adhering to ISO standards, conducting ongoing training, and implementing rigorous risk assessments and equipment inspections. Our protocols help protect both our team and our clients’ projects.
How Hard Bakka Rigging Ensures Safety in Every Project
At Hard Bakka Rigging, safety is our top priority. Our experienced team undergoes precise training to minimize risks. By working together, we can form a safer working environment for everyone involved in rigging operations.